class=”sc-3778e872-0 gWjAEa”>
A thud and splinters of wood splashed onto the table. “Would you like to?” Bentley employee John grins and hands us a very sharp crowbar and a hammer. How do you smoothly cut wood veneer strips at a 90 degree angle? Stack them so that the protrusion is at right angles, apply the chisel diagonally and boom – the coating will slide. Both strips were ready for the box and the thumb was still somehow between the two.
That’s why Bentley prefers the interior of its car to be done by professionals. The 104-year-old British automaker has been part of the VW Group since 1998 after a bizarre takeover battle with BMW. As in the past, craftsmanship is still required when carts are turned into wheeled saloons with leather, wood, metal and fabric. But even luxury car brands have to keep up with the times. Instead of lords and ladies, young start-up founders from the USA, China or the Middle East have long been shown how to decorate their new cars in an individual one-off at the main factory in Crewe (England). In the past, a kilo of wood was more or less irrelevant. But these customers are now asking questions about the sustainable circular economy, vegan leather and eco-friendly production.
Refinement creates profit
And neatly puts a checkmark on the list of options. 90 percent of all Bentleys delivered are customized; Even expensive details are ordered three or four times more often than CEO Adrian Hallmark (61) expects. The result was 2022, a record third in a row, crowned with an 82 percent increase in profit compared to 2021. Mulliner’s in-house finishing department contributed less than five percent, but sold five times more than three. Years ago.
The cars come off the assembly line here, as in every VW group factory, but only a lone robot does the job of gluing the windshields. Otherwise, the rules of manual work – until the last inspection, which people still do more meticulously than machines. And no robot can do it as perfectly as a tailor can embroider 133 meters of sewing thread for four door panels in 135 minutes. During the 95 hour assembly time per car – without customisation – the labor costs are very high, explaining a significant part of the price level at the Bentley: it doesn’t get much cheaper than around 190,000 francs.
Thin veneers are stacked in the air-conditioned wood workshop. California redwood, Spanish oak or swamp wood, preserved in mud for centuries, is turned into instrument panels by baking them with aluminum supports and cardboard at 145 degrees Celsius and 200 bar pressure. The very thin veneers save a lot of material, again being cut in half lengthwise and then unrolled to appear as one continuous piece. John teaches about grain directions, round, cross and cake cuts, and how each wood needs its own treatment. Dream: “Forest Scout in Hawaii.” For Bentley of course. After painting or buffing – high gloss paints are not better suited for beginner customers – it’s time to polish. Again and again, to the point of absolute perfection.
Manual work and digitization
But digitization is entering the factory. 3D printers produce customized parts for half the cost of regular injection molding. Lasers cut wood and artificial intelligence (AI) helps cut leather for seats and doors. In the past, cows used to make leather were kept in laboratory conditions so that neither barbed wire nor mosquito bites would damage their skin. Today they live freely in the pasture. Employees spot scars and quirks on the skin and mark them with chalk. An AI then scans the leather and places patterns for seat covers and panels with only minimal waste. For example, it is embroidered on key chains.
Beyond 100 is now Bentley’s strategy aimed at making luxury all-round sustainable: CO₂-neutral energy supply thanks to photovoltaics, full adherence to social and ethical standards by all suppliers, and careful use of resources. A challenge, in particular, with the electrification of drives planned by 2030, because the source of every gram of battery lithium must be traceable. Facilities and processes are currently being planned for new production in the old halls. As the paint shop is the bottleneck, more than 15,000 cars will be produced annually in the future.
Race cars and luxury coupés
Great art is in Mulliner. Here, special series such as Bacalar (starting from CHF 1.7 million) and Batur (starting from CHF 1.9 million) are produced on the basis of Continental GT, right next to the factory, and customer demands that are not in any catalog are met. You feel like you’re traveling back in time: half a dozen Bentley Blowers and Speed Sixes – remakes of historic race cars from the 1930s – were hand nailed, riveted and screwed together. The only concessions to modernity are fire extinguishers and safety tanks that meet today’s racing regulations. Famous customers? Weird special requests? Mulliner’s boss, Paul Dickinson, is speechless. Confidentiality is a matter of honor so as not to offend customers. But his advisors could still point the most ridiculous design ideas on the right track.
But then he shows off his group’s latest work ready for delivery: a seal gray Continental GT with a neon green interior. You are allowed to be amazed but unfortunately photos are not allowed. The best workmanship. But taste can still be a matter of luck.
Source: Blick
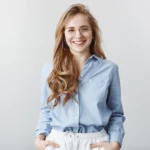
I’m Ella Sammie, author specializing in the Technology sector. I have been writing for 24 Instatnt News since 2020, and am passionate about staying up to date with the latest developments in this ever-changing industry.