class=”sc-3778e872-0 gWjAEa”>
Until a few years ago, the tire world was still running on an orderly, well-known path: First of all, it was important for manufacturers to create as much grip and stable running behavior on the tire as possible. By using materials such as natural rubber or steel, these properties can be applied efficiently.
But sustainability is playing an increasingly important role not only for automakers, but also for tire manufacturers. The point is this: not just the production itself, but the CO2– Become both neutral and end product with the use of ecological and recyclable components. Manufacturers like Michelin and Continental are striving to achieve a positive climate balance by 2050.
big challenges
The art of using sustainable materials is to preserve defining characteristics such as grip and rolling resistance, especially in a safety-related component such as tyres. The material must remain elastic and strong so that it does not break apart during braking or sudden acceleration. Even eco tires have to do what their less sustainable predecessors promised, on dry and wet roads as well as winter snow and ice. In short: environmental protection should not come at the expense of safety.
Of course, this process towards sustainable tires is not completed overnight. The transformation will happen step by step. For example, Continental tires currently consist of up to 20 percent renewable or recyclable materials.
Green Gum
If tires are to become more sustainable, manufacturers need to focus on one product in particular: natural rubber. It is often grown in monocultures in southern countries with the use of pesticides. Since a car tire consists of up to 40 percent rubber, it has to be imported in huge quantities. The good news: Tire manufacturers are working relentlessly to find sustainable alternatives with first results.
An example is the Finnish company Nokian Tires, which is currently researching synthetic rubber from birch bark residues. Enough raw materials will be available: birch bark is a waste product of the pulp, paper and plywood industries. According to manufacturer Reselo, the forest industry in Finland and Sweden alone produces enough raw materials to produce 200,000 tons of birch rubber. Another variant is rubber made from dandelion.
However, these alternatives can replace previous materials only if they have the same or at least similar properties. The same is true for silica: the refractory building material binds materials in rubber better, which minimizes wear. The compound also affects a tire’s handling, rolling resistance and mileage. Traditionally, the fabric is made of quartz sand. However, it is more energy efficient to obtain it from rice husk ash.
keyword recycling
The tire production of the future will also include recycled PET bottles in the form of reclaimed rubber and HMLS polyester yarn. The material supports safety at high driving speeds and remains dimensionally stable even under load and high temperatures. The materials used in coated tires are already taken from shoe soles and artificial turf. And steel can already be made with hydrogen from renewable energies instead of conventional CO.2– Dense coal is produced.
The sustainability strategy of tire production also includes transparency and traceability of the materials used. Because if there is CO, all ideas and concepts gush out.2 is blown into a large amount of air. It is clear that the future of tires will be shaped in the laboratory as well as on the test tracks.
Source: Blick
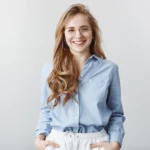
I’m Ella Sammie, author specializing in the Technology sector. I have been writing for 24 Instatnt News since 2020, and am passionate about staying up to date with the latest developments in this ever-changing industry.